長沙專業(yè)工廠MES系統(tǒng)廠家
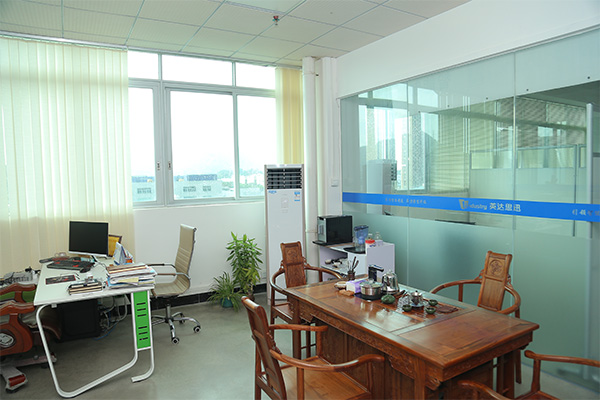
的行業(yè)性需求與通用型產(chǎn)品之間的矛盾日漸突出,產(chǎn)品化程度不夠。與ERP不同,MES系統(tǒng)從產(chǎn)生開始,就是為了解決通用型的ERP功能難以解決的工廠管控問題,因此,即使有多年的發(fā)展,也無法擺脫行業(yè)性對其形成的局限。MES系統(tǒng)在進行排產(chǎn)計算的過程中需要提取物料的預(yù)計庫存數(shù)量,才能保證原材料的供應(yīng)滿足生產(chǎn)需求。需要注意的是:這個預(yù)計庫存數(shù)量與ERP庫存模塊所提供的庫存數(shù)量有本質(zhì)的區(qū)別。
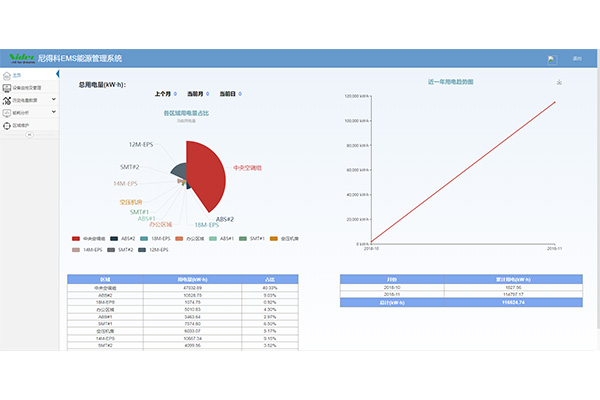
工廠在實際生產(chǎn)過程中,一旦生產(chǎn)過程無法嚴格把控管理,專業(yè)工廠MES系統(tǒng)質(zhì)檢過程就很容易出現(xiàn)不合格產(chǎn)品,工廠MES系統(tǒng)廠家為了合理的管理這些產(chǎn)品,可以通過mes生產(chǎn)管理系統(tǒng)將產(chǎn)品進行分類,提供生產(chǎn)質(zhì)檢和委外質(zhì)檢,自定義設(shè)置質(zhì)檢字段、編號、類型、等級,支持質(zhì)檢單跟進、合格品入庫、不合格品返修,降低廢品率,為企業(yè)節(jié)約成本。
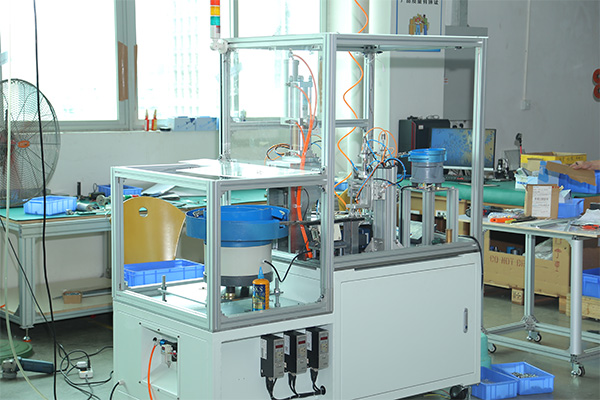
的智能制造的廣泛普及和應(yīng)用對MES系統(tǒng)提出了更高的要求,如生產(chǎn)的靈活性、可擴展性、開放性、快速的重構(gòu)和對市場變化的響應(yīng)。因此,MES系統(tǒng)的標準化應(yīng)沿著以下幾條線進行:體系結(jié)構(gòu)的標準化、業(yè)務(wù)邏輯的建模和標準化、信息結(jié)構(gòu)的標準化。
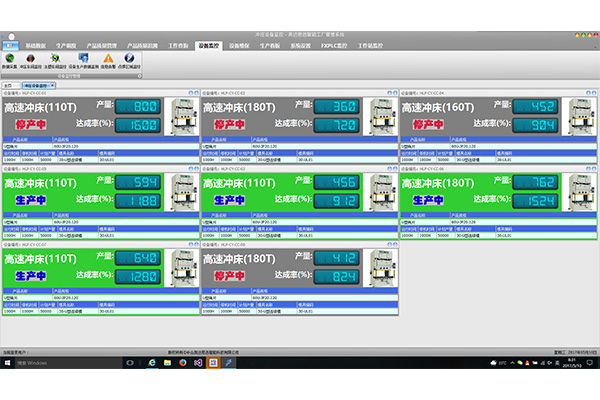
實施期間,技術(shù)風險可能導(dǎo)致性能損失或計劃要求延遲。一個常見的原因是在實現(xiàn)過程中配置和范圍蔓延。不斷添加和更改實現(xiàn)的要求可能會對相關(guān)功能的不同區(qū)域中的配置之間的關(guān)系產(chǎn)生不利影響。每次改變都會產(chǎn)生負面的連鎖反應(yīng)和后果。通過量身定制的解決方案,這些風險可能更高,因為配置是解決方案的關(guān)鍵,如果不遵循或操作一套標準,就會有更多的失敗空間。
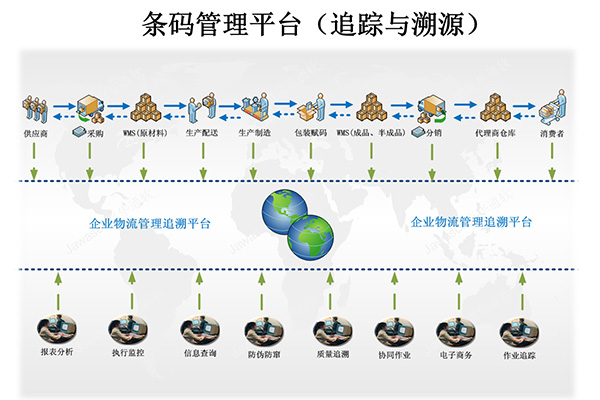
在對MES系統(tǒng)信息化的建設(shè)投資的時候,往往會投入上百萬上千萬。所以要保證這么大的投入要能有穩(wěn)定的回報的話,加強對階段化成果的重視是相當重要的,這就需要企業(yè)在信息化建設(shè)的過程中能有效合理地計劃安排整個項目工程,并對階段化的成果進行仔細分析,來保證在以后的實施過程中能取得更大的成效。